I saw a guy using a plexie glass box that held a loop of about 2 min of film that allowed him to play this loop continuously without the need of rewinding. The box seemed to cause the film to loop inside the plastic compartment. Is thier anyone familiar with such a device and some instructions, diagrams, ect on how to build such a device. I 'm using two super 8mm projectors in a display that are motion activated, and this type of looping would really make the project work.
G. Kern
Plexie Glass Looping Mechanism
Moderator: Andreas Wideroe
- MovieStuff
- Posts: 6135
- Joined: Wed May 01, 2002 1:07 am
- Real name: Roger Evans
- Location: Kerrville, Texas
- Contact:
He was probably using a Fairchild display unit. These were pretty typical back in the 70's and could also play sound stiped film. However, because the film was stored like an 8-track (where the film winds on the outside and comes out the middle of the core) films used this way typically had a pretty short life and got scratched pretty easily.
If you film isn't too long, you can make a continuous loop cabinet that sits above your projector. Basically it is a series of rollers that the film loops back and forth on in kind of a zig zag pattern. This is how Disney engineers solved the continuous loop problem in the early days of Disneyland before the advent of practical video or hard drives.
The rollers can be made by using three different size washers stacked end to end. A large fender washer goes on each end. The slightly smaller washers (ideally plastic) go on next in line from each side and smaller metal washers are placed inbetween, using enough so that the proper width is attained. The film will ride between the two outer washers but on top of the two plastic washers so that the image area is never touched. The assembly is simply put on a shoulder bolt of the appropriate diameter that is screwed into the wooden panel holding the rest of the the rollers in a zig-zag pattern.
I built one long ago for 16mm and was able to fit a 100 foot roll in a space about 2.5 feet wide by 3 feet high. Total material cost was less than $100 but it was not covered with a plexiglass lid, though I doubt that would add much to the cost. The panel was only about 2 inches thick and sat above the 16mm projector on its own feet which extended down to the table top. The film was threaded through the projector like normal and then looped back and forth along the rollers, making its way to the top. Then the film was brought back down to the input of the projector where it was spliced to the tail to form a continous loop.
The other advantage of using the rollers is that the film never gets stacked on top of itself, which it does in the Fairchild or any other projector. Stacking is what causes the majority of scratches and abrasions on film because dust gets trapped between the film. As the film "cinches" the dust particles will dig in and cause thousands of tiny scratches in both the base and emulsion. The rollers ideally handle the film only by the edges so the film is only in contact with air as it moves back and forth along its path. Having a plexiglass enclosure around the film will also help keep the dust off, though it's inevitable that it will need to be cleaned every so often.
If you're serious about how to construct one, I could post some drawings.
Roger
If you film isn't too long, you can make a continuous loop cabinet that sits above your projector. Basically it is a series of rollers that the film loops back and forth on in kind of a zig zag pattern. This is how Disney engineers solved the continuous loop problem in the early days of Disneyland before the advent of practical video or hard drives.
The rollers can be made by using three different size washers stacked end to end. A large fender washer goes on each end. The slightly smaller washers (ideally plastic) go on next in line from each side and smaller metal washers are placed inbetween, using enough so that the proper width is attained. The film will ride between the two outer washers but on top of the two plastic washers so that the image area is never touched. The assembly is simply put on a shoulder bolt of the appropriate diameter that is screwed into the wooden panel holding the rest of the the rollers in a zig-zag pattern.
I built one long ago for 16mm and was able to fit a 100 foot roll in a space about 2.5 feet wide by 3 feet high. Total material cost was less than $100 but it was not covered with a plexiglass lid, though I doubt that would add much to the cost. The panel was only about 2 inches thick and sat above the 16mm projector on its own feet which extended down to the table top. The film was threaded through the projector like normal and then looped back and forth along the rollers, making its way to the top. Then the film was brought back down to the input of the projector where it was spliced to the tail to form a continous loop.
The other advantage of using the rollers is that the film never gets stacked on top of itself, which it does in the Fairchild or any other projector. Stacking is what causes the majority of scratches and abrasions on film because dust gets trapped between the film. As the film "cinches" the dust particles will dig in and cause thousands of tiny scratches in both the base and emulsion. The rollers ideally handle the film only by the edges so the film is only in contact with air as it moves back and forth along its path. Having a plexiglass enclosure around the film will also help keep the dust off, though it's inevitable that it will need to be cleaned every so often.
If you're serious about how to construct one, I could post some drawings.
Roger
Directions would be Great.
If you could post some directions on how to build the looping mechanism that would be great. I using two super 8mm projectors in a display that is activated by motion detectors when an individual enters ther room. So any directions would be most hopeful.
Thanks
G. Kern
Thanks
G. Kern
- MovieStuff
- Posts: 6135
- Joined: Wed May 01, 2002 1:07 am
- Real name: Roger Evans
- Location: Kerrville, Texas
- Contact:
Okay, here are some quick drawings that show the relationship of the looping mechanism to the projector as well as the contstruction of the individual rollers using washers on a bolt with a T-nut holding it to the panel with all the other rollers. There are three different size of washers and they can all be metal though plastic or rubber would be best for the ones that form the shoulder the film rides on. Use enough smaller washers in between to keep the rubber washers separated so that the film is handled only by the edges. The two outer washers are "fender" type washers that keep the film from coming off the roller. These need to be as big as possible to keep accidental spills from happening if the film breaks and tension is lost.
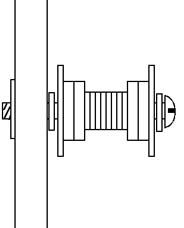
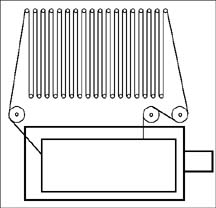
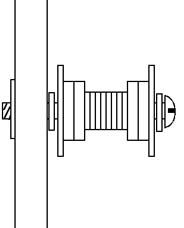
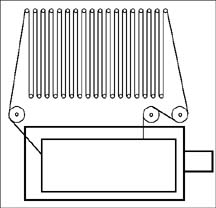
- MovieStuff
- Posts: 6135
- Joined: Wed May 01, 2002 1:07 am
- Real name: Roger Evans
- Location: Kerrville, Texas
- Contact:
I should clarify that once the correct number of washers are configured, you will need to glue them together with a very light coating of epoxy so they will not separate. Having these type of roller machined out of Delron is best but making them yourself like this will work just as good. Also, there should be a nut separating the roller from the mounting panel. The nut is on the roller side and the T-nut is on the back side of the panel. The nut is necessary to tighten against the T-nut. The head of the bolt will keep the roller from coming off. The larger rollers that guide the film into and out of the projector are just larger versions of this same assembly.
The number of rollers and the height of the panel will determine how many feet of film you can span. This should only be used on projectors that have a sprocket feed. Sprocketless projectors should not be used as the spanning will put too much back tension on the film for the advance claw to overcome.
Roger
The number of rollers and the height of the panel will determine how many feet of film you can span. This should only be used on projectors that have a sprocket feed. Sprocketless projectors should not be used as the spanning will put too much back tension on the film for the advance claw to overcome.
Roger
Other looping mechanisms for 8 & 16mm
Anyone know the name of this piece of equipment. I'd like to look for other design types. I have heard of units that can hold up to 1/2 hour of film.
G. kern
G. kern